Aggregate Screening Plant
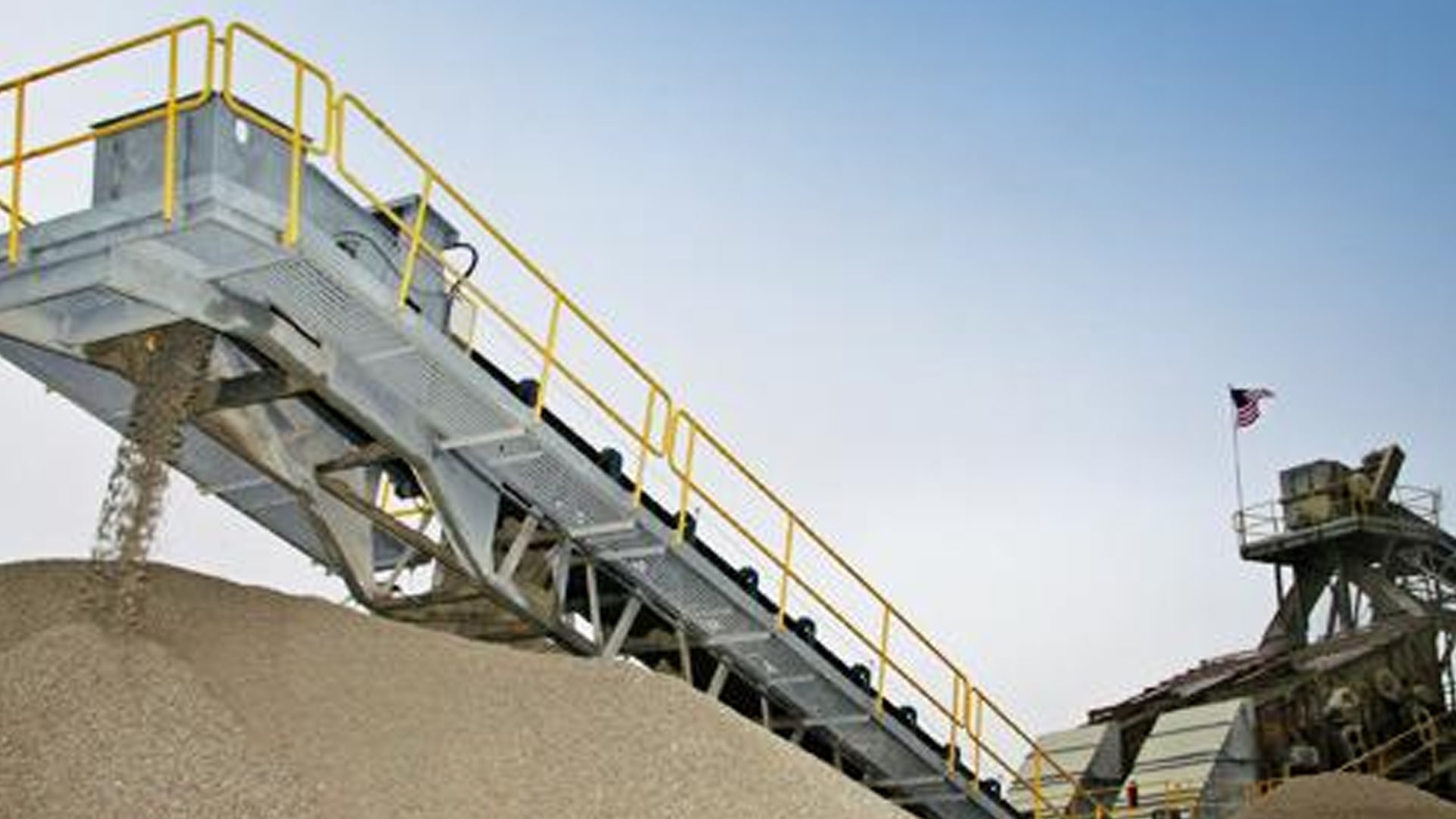
Elevate reliability with hot-dip galvanizing
Galvanized: 2010
This constant abrasion can only be fought off by the powerful barrier and cathodic protection of hot-dip galvanized (HDG) steel. The zinc-iron alloy layers created during the galvanizing process become harder than the steel itself. The metallurgically bonded zinc iron alloy will protect the structure for decades from nicks, chips and the harsh winters.
The manufacturer was impressed by the AGA life cycle cost calculator, which reveals the savings of hot-dip galvanized steel over the life of a project. While the initial cost was competitive with paint, the life cycle cost was miniscule in comparison to what the ongoing maintenance would be on a painted structure in this harsh environment. Hands down, HDG was the most cost effective solution.
The screening plant is in a constant state of vibration, requiring precision for all bolt together assemblies. AZZ provided uniformity for all ladders, stairs and platforms ensuring solid connections that will remain corrosion free. More than 200 tons of screen tower, splitter feed chutes, gathering conveyors, stockpile conveyors and walkway platforms were galvanized. AZZ offered a customized turnaround time that allowed extra time to install auxiliary motors, liners and belts. In turn, the manufacturer was able to deliver the finished product on time.
The cathodic protection of the zinc coating makes a strong visual statement of durability and superior protection. Since HDG steel is the most recycled product in the world, this project site can be a part of the sustainable development of the area. All of their requirements for durability, sustainability and environmental friendliness were accomplished with hot-dip galvanizing.
Contact Us
Email Signup
Sign up to receive the latest news from AZZ