Henderson County Mine Conveyor
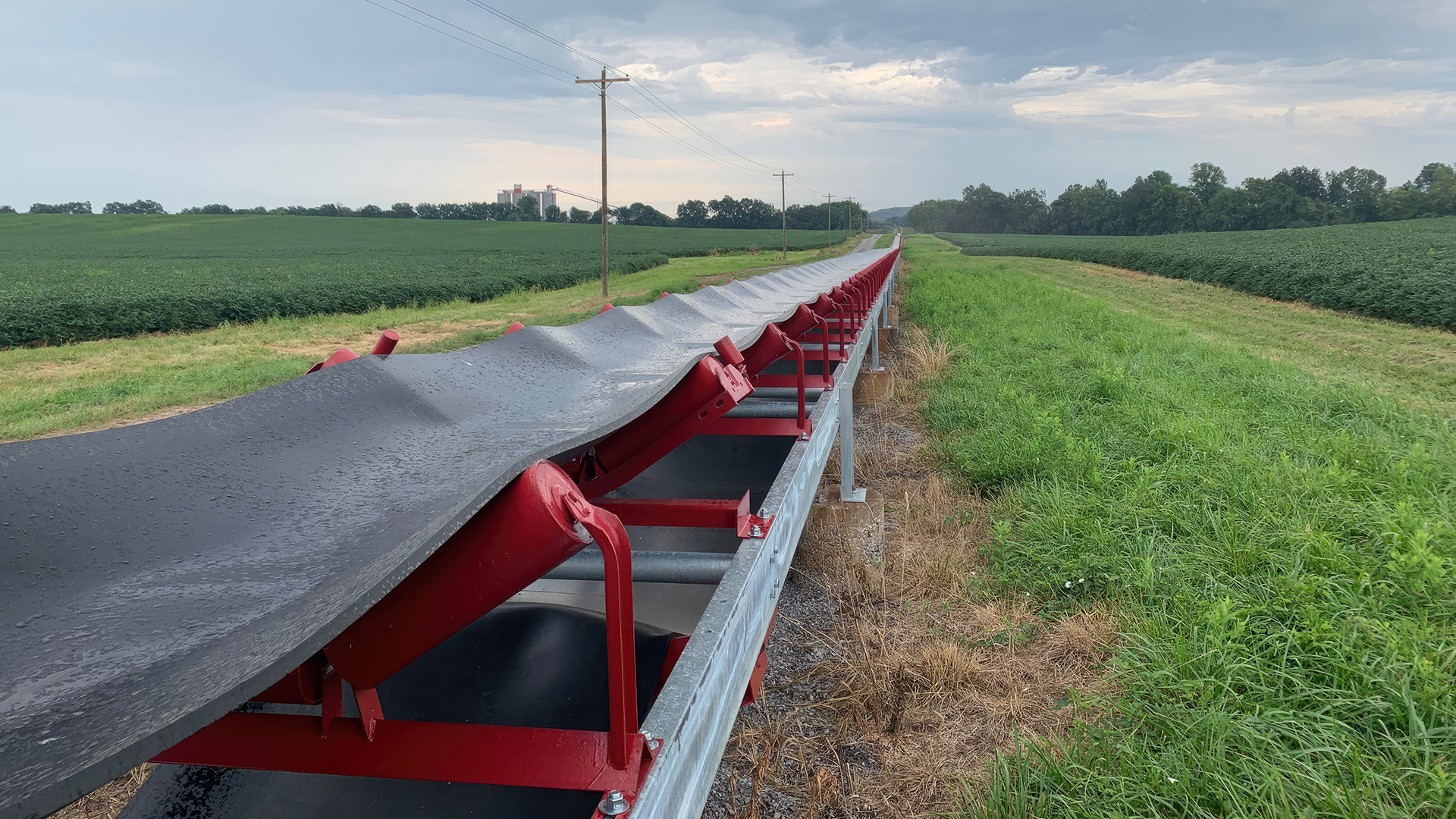
As industrialization took hold, the demand for coal increased dramatically. Railroads and other industries required coal as a source of fuel, leading to the expansion of mining operations. Kentucky’s vast coal reserves, especially in the Appalachian region, attracted significant investment and development, and Kentucky has since become the 4th largest coal producer in the nation.
In the far western part of the state, River View Coal LLC, a subsidiary of Alliance Coal LLC, has been operating River View Mine in Union County since 2009. This is the largest room-and-pillar underground mine in North America, capable of producing 2,700 tons per hour. Just 11 miles away from this site is the future home of Henderson County Mine, expected to be fully operational by January 2025. This will be Alliance’s first venture into neighboring Henderson County. As with most ambitious projects, this new venture posed a list of challenges. The first phase involved the removal, upgrade, and replacement of roughly 6 miles of old conveyor line to be used for taking coal to the nearby Ohio River.
Massive in scale, the overland conveyor system consists of a series of interconnected belts and supporting structures that move the coal from one point to another. Adding to the complex nature of the project, the new conveyor lines were designed to utilize existing footers, bridges, and transfer station structures when possible. The threat of corrosion also loomed large. The system is constantly exposed to rain, snow, humidity, and other forms of moisture. Conveyor structures and components can have crevices, joints, and hard-to-reach areas where moisture can become trapped. These areas create ideal conditions for corrosion to develop unseen. Additionally, conveyors experience mechanical stresses due to the movement of materials and the operation of the system. Vibrations and impacts can damage protective coatings, leading to the initiation of corrosion. Even the coal being transported has been shown to be corrosive. Finally, the rugged and remote location of the project means that future maintenance projects will be expensive and challenging. As it is vitally important that the intricate network of conveyors and supporting infrastructure operate reliably, year after year, in all weather and operating conditions, downtime for frequent maintenance was not an option.
With these challenges in mind, the decision to use hot-dip galvanized components was an easy one. Galvanizing provides numerous advantages over other coating methods when used in harsh mining environments, including superior abrasion resistance, extended time to first maintenance, and resistance to moisture trapping and temperature fluctuations. Galvanized coatings can last for decades, even in tough conditions. The extended lifespan of galvanized structures reduces the need for frequent replacements and repairs. This directly translates to lower material and labor costs over the long term. It was also recognized that corrosion-related failures can lead to secondary costs such as environmental cleanup, safety hazards, and legal liabilities. By preventing or minimizing corrosion, hot-dip galvanizing helps avoid these additional expenses and results in the most cost-effective solution over the operating life of the conveyor system.
Ultimately, one million pounds of material, including legs, frame channels, and return idlers, were galvanized as part of this complex and challenging project. The production and installation took the crew almost a year to complete and will be used by the 260 future workers at the Henderson County Mine once fully operational. Thanks to the selection of hot-dip galvanizing, the conveyor system should reliably transport the region’s vital coal for many years to come!
Galvanizing provides numerous advantages over other coating methods when used in harsh mining environments, including superior abrasion resistance, extended time to first maintenance, and resistance to moisture trapping and temperature fluctuations.
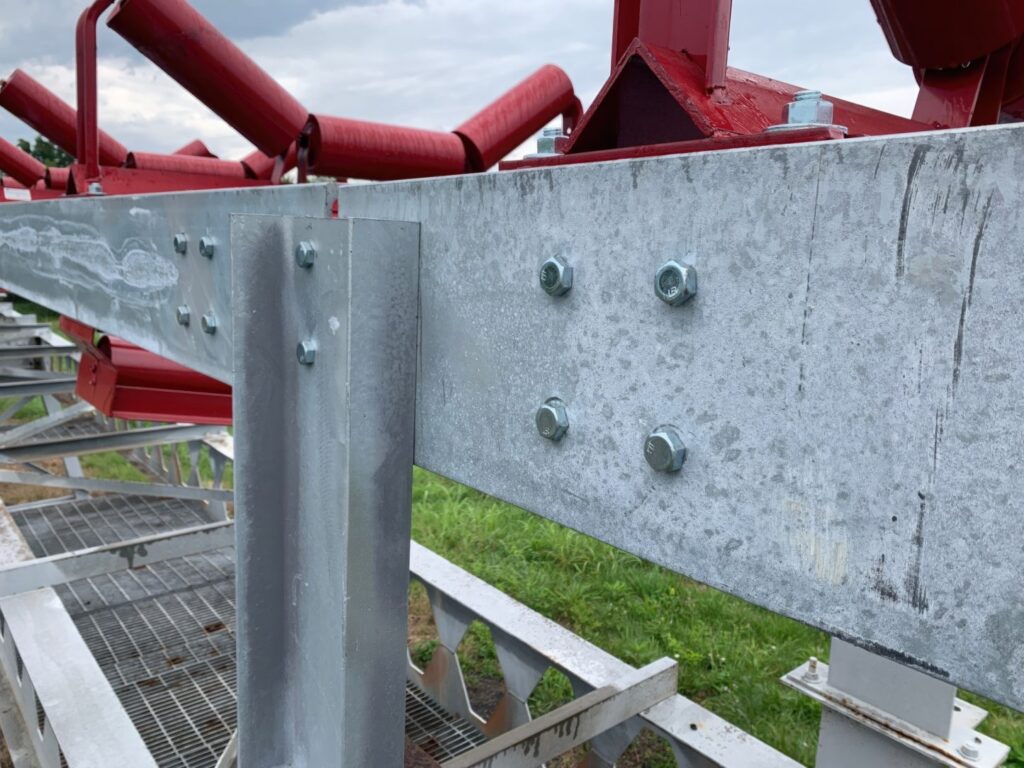
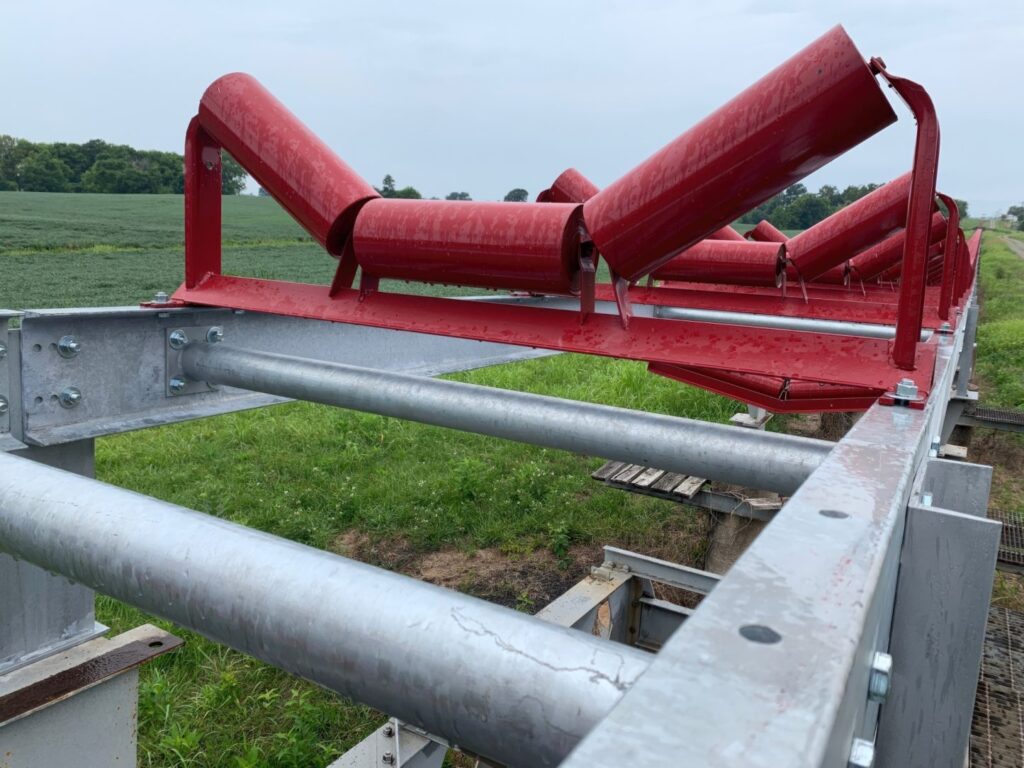
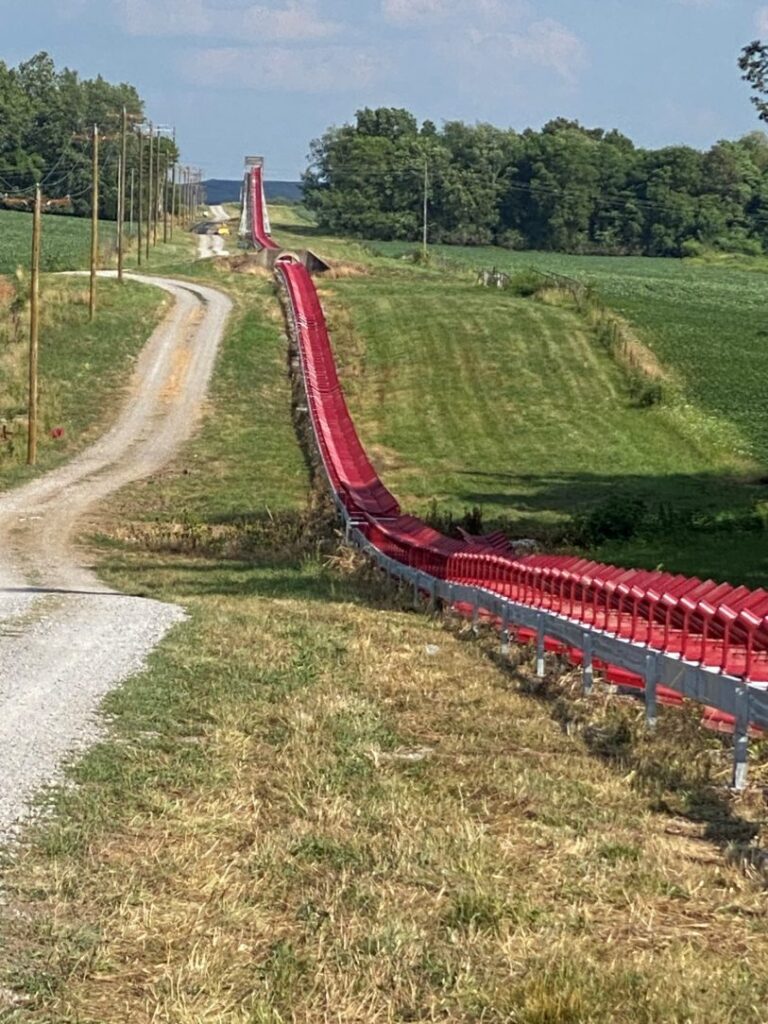

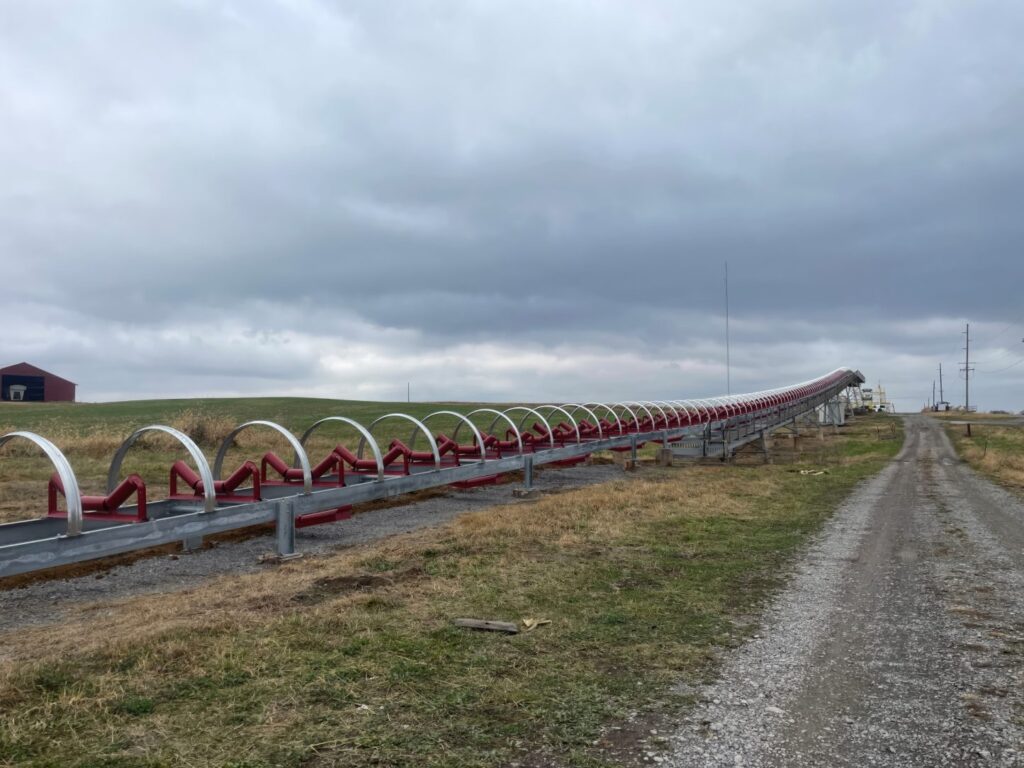
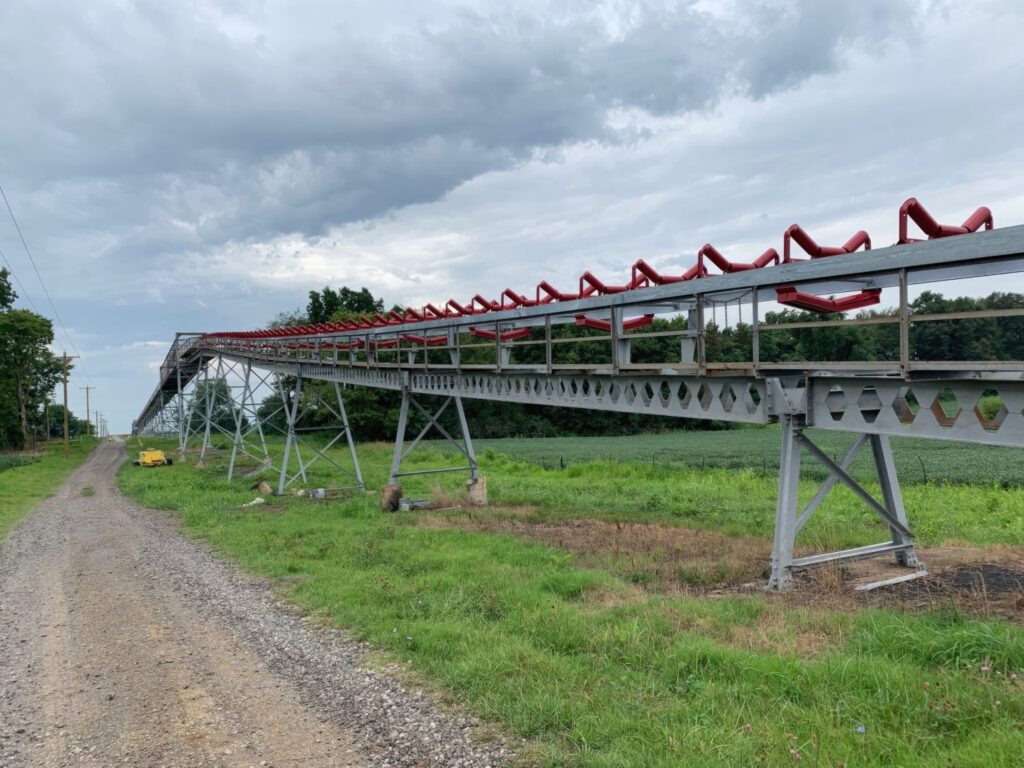
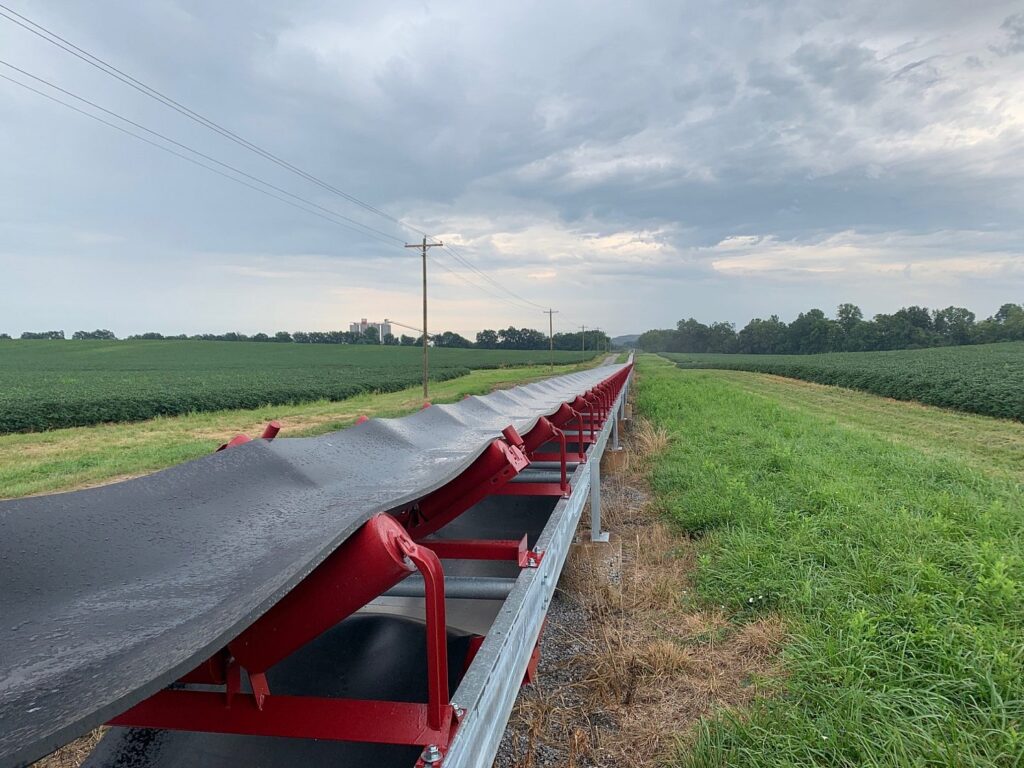
Contact Us
Email Signup
Sign up to receive the latest news from AZZ