Oil Bridge
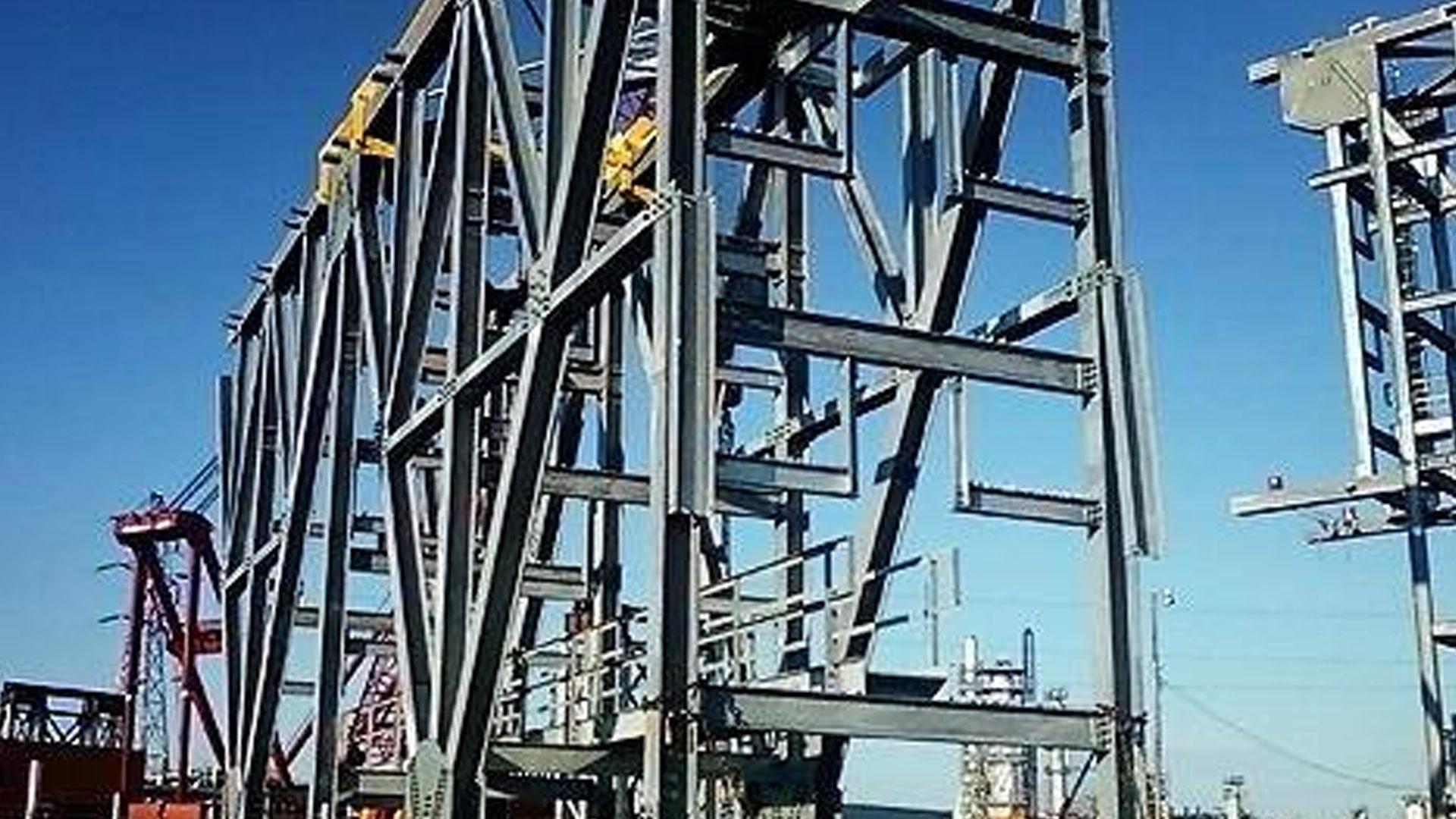
Maintenance-free for generations
Date galvanized: 2010
With a rigorous and intensive production schedule, the bridge was able to take advantage of the quick turnaround provided by the hot-dip galvanizing process.
Over the years, expansion of the oil refinery was limited. The industrial property owned by the company is split into two tracts divided by a span of railroad tracks. Economic conditions led management to link the two tracts in an effort to expand production capacities and create new jobs for the local market. Time and budget constraints dictated a bridge carrying large pipes over the tracks was the most viable option for connecting the two tracts.
Limited access to the private railroad property meant it was first necessary to pre-construct the bridge, and then lift it into place in large sections. The steel elements were first speedily hot-dip galvanized by AZZ before preconstruction. The galvanizing process was performed indoors, independent of weather, allowing for the quick turnaround necessary to keep a project on schedule. The structure was then assembled, disassembled, shipped and reassembled before being lifted into place by cranes.
Because of the restrictions of private property access and the need for speedy installation, there would be no time for coating touch-up, nor was there access once installed. Paint for corrosion protection would have required such efforts, both initially and continuously throughout the life of the structure. Because future access to the bridge was not guaranteed, the construction needed a maintenance-free corrosion protection system – hot-dip galvanized steel meets this requirement.
Located in the harshest of the five environmental categories – industrial – the bridge needed durable, long-lasting protection for the 950 tons of structural steel ladders, handrails, sheet steel and fasteners. The tough zinc coating, which is more difficult to penetrate than the substrate steel itself, will protect the bridge from nicks and scratches caused by flying gravel or daily wear-and-tear.
The project serves as a testament to the quick turn time and superior corrosion protection of hot-dip galvanized steel. Because the pieces could be galvanized and immediately put into the field, crews were in and out of the private property in short order, while the bridge will provide years of maintenance-free service to the refiner. Hot-dip galvanized steel will keep this structure standing strong and rust free for decades to come.
Contact Us
Email Signup
Sign up to receive the latest news from AZZ