Quarry Conveyor
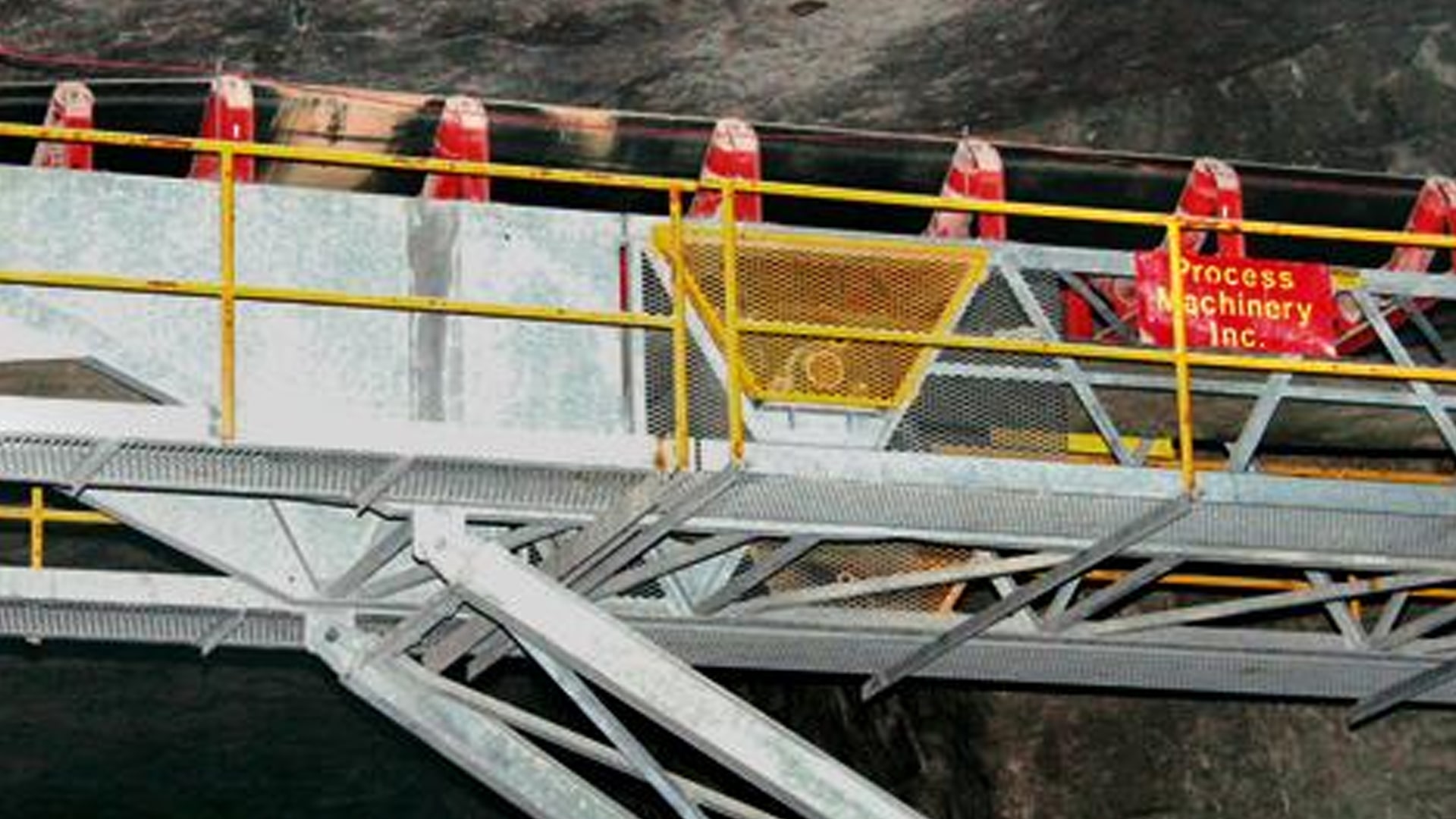
Hands down galvanizing is the most cost-effective solution
Limestone pieces range from unusually large to extremely small particles. The conveyor system in the quarry required a coating that could withstand the constant bombardment of small particles and the moisture associated with the underground environment. Understanding the benefits of hot-dip galvanizing, the fabricator felt confident they were providing their customer with the most durable coating option available for this unique setting.
In the underground environment, the conveyor system is also subject to constant exposure to humidity and moisture. HDG provides the necessary corrosion performance to withstand these harsh conditions. With the metallurgically bonded zinc coating protecting all surfaces and the sacrificial properties of zinc self-healing all nicks and chips, the system is receiving the ultimate in coating protection.
While the initial cost of HDG was higher than paint, the life-cycle cost was miniscule in comparison to what the maintenance cost would be on a painted structure in this environment. The conveyor moves material across 4,560 feet, making some portions inaccessible for future maintenance. HDG eliminates the need for maintenance in these areas. Attempting to maintain a painted structure in this environment would be costly and difficult due to the dust factor and humidity. Hands down, HDG was the ultimate choice.
Having a long service-life that required minimal maintenance was critical to the end user. The estimated 75-year service life of the HDG coating for the project will most likely outlast the life of the quarry.
Contact Us
Email Signup
Sign up to receive the latest news from AZZ