Racetrack
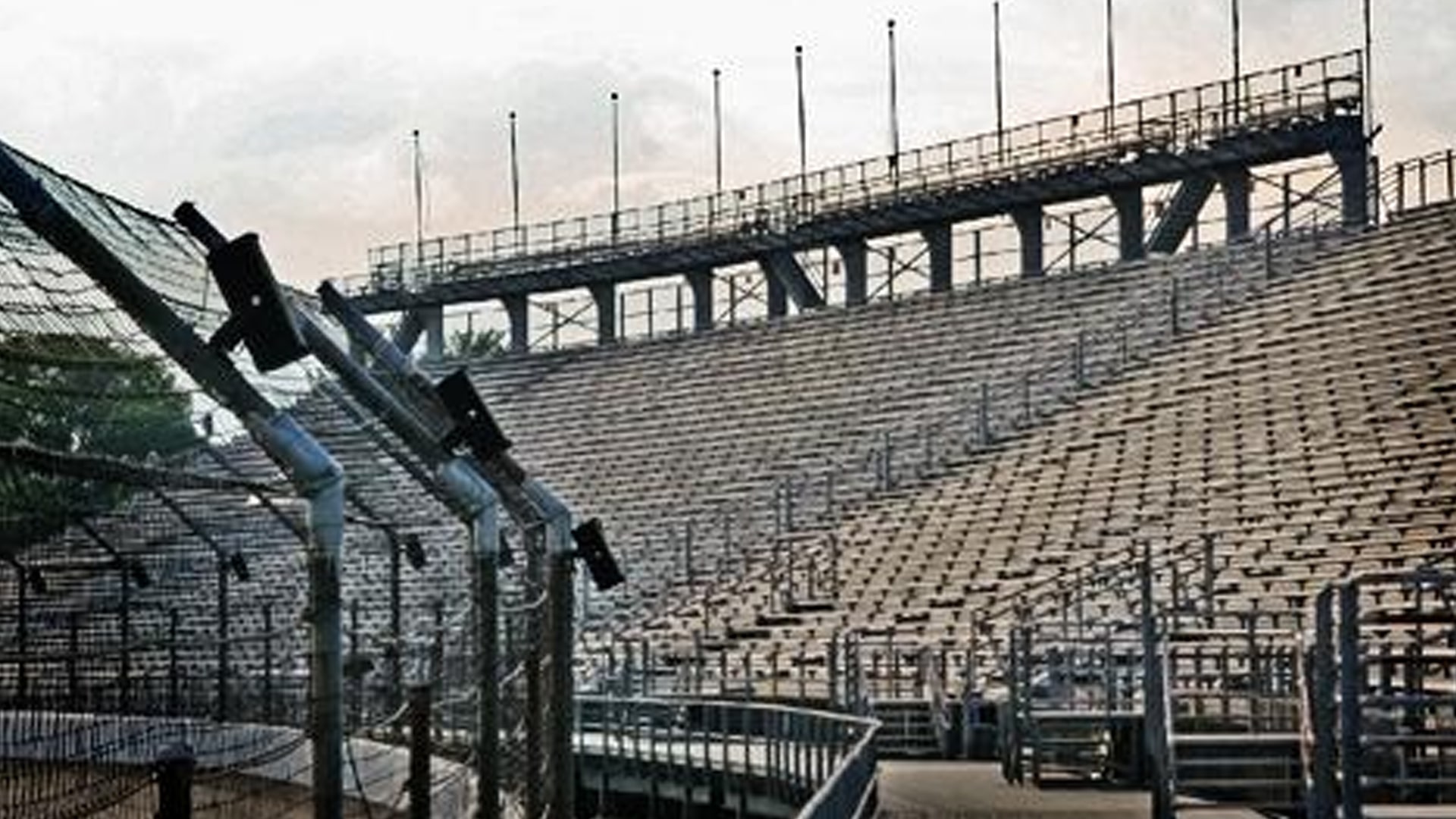
Protecting an American icon
Galvanized: 1991
As a result, it was necessary to hire a full-time crew of men to move from one section to another, providing year-round maintenance and upkeep on the deteriorating paint job.
The cost of perpetual painting was overwhelming, with no end in sight. Finally, in 1991, they decided to test hot-dip galvanized steel by incorporating it into the new construction being built on a turn. A thousand tons of steel bleachers were galvanized, with great success. After a year of maintenance-free corrosion protection using galvanized steel, the owners realized it would be more cost-effective over the life of the structure. They decided to tear down the steel elements, sandblast the failed paint system and galvanize them one section at a time.
While the cost of incorporating galvanized steel was competitive initially, the long-term cost-effectiveness has proven to be an enormous savings, over the past 19 years. When the sections were first galvanized in 1991, the mil readings indicated excellent coverage of the steel. Over the decades, the galvanized steel has stood strong and maintenance-free, earning every penny back of the initial investment. Because of this proven performance, the owners set a goal to galvanize one section of bleachers each year between scheduled events—eventually the whole structure would benefit from peerless corrosion protection.
Subject to the abrasive foot traffic of millions of race fans every year, the stadium needed maintenance-free protection from unsafe and unsightly corrosion. In a corrosive industrial atmosphere with race track emissions and exposure to harsh midwest winters, rain and sun, the bleachers have taken advantage of the superior barrier and cathodic protection created during the galvanizing process.
The formation of the zinc patina has turned the steel to a uniform and traditional matte gray color well suited to the urban surroundings and raceway environment. The zinc patina is the formation of zinc corrosion byproducts on the surface of the steel. Zinc, like all metals, begins to corrode when exposed. As galvanized coatings are exposed to both moisture and free flowing air, the corrosion byproducts will naturally form on the coating surface. The zinc coating acts as a barrier against the penetration of water, oxygen and atmospheric pollutants, cathodically protecting the steel from coating imperfections caused by nicks or abrasions.
The patina is impervious and passive, which slows the corrosion rate of the zinc, thus providing long-lasting protection from damaging rust. Proving the durable nature of galvanized steel, a study conducted in 2009, indicates little or no zinc lost since the initial galvanizing in 1991. The coating is still well above the minimum ASTM coating thickness required by ASTM A123–still working hard to protect the steel from corrosion, without maintenance.
Contact Us
Email Signup
Sign up to receive the latest news from AZZ